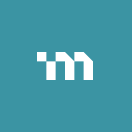
Here We Go Again With the Medical Device Excise Tax
March 13, 2018
By Cindy Fazzi
When the medical device excise tax was suspended recently, the industry was left with a sense of déjà vu. Between January 2013 and January 2018, the tax was implemented once and frozen twice. How long will this touch-and-go situation continue?
Full story